In the competitive world of battery manufacturing, the quality and safety of products are paramount. At EVE, the production of 3.2V LiFePO4 battery is upheld to the highest standards, largely due to the crucial role played by their state-of-the-art Testing Center. This facility is not just a part of the production line; it is a cornerstone of EVE‘s commitment to excellence. Let’s delve into how the Testing Center contributes to the perfection of EVE’s 3.2V LiFePO4 batteries.
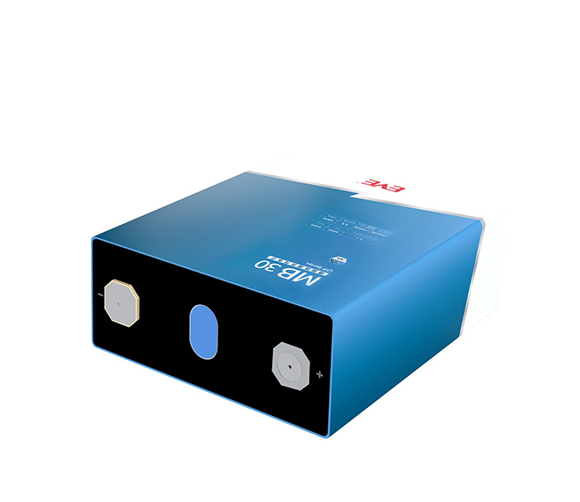
Comprehensive Testing Across Four Key Dimensions
1. Materials Testing
The foundation of any high-quality battery lies in the purity and suitability of its materials. At EVE’s Testing Center, the journey towards perfection begins with rigorous testing of the raw materials used in battery production. This ensures that only the best, most consistent materials are used, setting the stage for reliable and safe battery performance.
2. Electrical Performance Testing
Once the batteries are assembled, their electrical performance is meticulously evaluated. This includes testing for capacity, voltage consistency, and power outputs under various conditions. These tests ascertain that each battery meets the stringent performance criteria required for market release.
3. Environmental Performance Testing
LiFePO4 batteries are celebrated for their robustness in diverse environmental conditions. To ensure this, EVE’s Testing Center conducts extensive environmental testing, exposing batteries to extreme temperatures, humidity levels, and mechanical stresses. This ensures that the batteries can withstand and perform reliably in any environmental condition they might encounter in real-world applications.
4. Safety Performance Testing
Safety is a non-negotiable aspect of battery manufacturing. The Testing Center performs a series of safety tests, including short-circuit, overcharge, over-discharge, and thermal runaway tests. These critical assessments help to prevent any safety incidents post-manufacture, ensuring that EVE’s batteries are not only efficient but also inherently safe.
IT-Driven Management and Calibration Excellence
All-Round IT-Based Management
EVE’s Testing Center is not just about manual checks and balances; it leverages an all-encompassing IT-based management system. This system oversees the operation of measuring instruments throughout the testing processes, enhancing the precision and reliability of the testing outcomes.
Calibration Protocols
Accuracy in testing is maintained through a rigorous calibration protocol where internal calibration is given priority. External calibration acts as a supplementary measure to ensure that every testing instrument is functioning at the highest standard. This dual approach to calibration helps maintain the integrity of testing results, ensuring that every battery that passes through has been evaluated under the most accurate conditions possible.
Conclusion: A Pillar of Quality Assurance
The Testing Center at EVE is more than just a facility; it is a testament to the company’s dedication to quality and safety. By thoroughly assessing every aspect of the 3.2V LiFePO4 batteries across materials, electrical, environmental, and safety performances, the center ensures that each product not only meets but often exceeds industry standards. This rigorous approach to production oversight is what sets EVE apart in the battery industry, solidifying its reputation as a leader in the production of safe, reliable, and high-performing batteries. Through the meticulous work conducted in the Testing Center, EVE continues to deliver products that are truly perfected for the market, ensuring customer satisfaction and safety in all applications.